广东南方某公司年产100万吨水泥生产线于2011年3月投产。水泥磨系统为两台Ф3.2 m×13 m球磨机加两台HFCG140-45辊压机的联合粉磨系统。随着生产设备的磨损、市场竞争的日益激烈,以及对能耗要求的不断提高,为了进一步提高水泥产能、降低电耗和节约成本,我公司于2017年针对开该系统展了一系列的技术改造,取得了预期效果。
1. 辊压机
水泥磨系统预粉磨采用HFCG140-45辊压机,辊面宽度仅450 mm,通过加宽辊面至550 mm使预粉磨效果得到提高,工作电流达到额定电流的65%左右,辊压机工作效率尚佳。经过多次对比与摸索,发现入辊压机下料管存在错位和尺寸偏小现象,导致物料进入辊压机时被迫做横向运动,填充区物料出现松散不密实状态;变向处的料压被管壁部分抵消,未完全作用于辊子,影响做功。
技术改造:通过将稳流仓整体平移使下料管与辊压机进料口对直;因下料管道尺寸为400 mm×400 mm,辊压机进料口尺寸为550 mm×550 mm,因此,将下料管增大至与辊压机进料口尺寸一致,并取消在管道内壁焊减磨圈的做法,使物料垂直下料增加料压,达到辊压机填充区物料密实的效果。改造后辊压机工作电流提高40~60 A,约占额定电流的70%左右,大大提高了辊压机的做功效率。入辊压机下料管改造前后对比见图2。
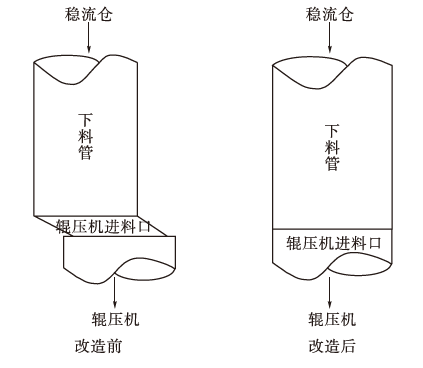
图2 入辊压机下料管改造前后示意
2 水泥磨隔仓板
该公司Φ3.2 m×13 m球磨机为三仓结构,一、二仓之间隔仓板为双层结构,二、三仓之间隔仓板为单层结构。一仓研磨体为钢球,二、三仓研磨体为钢段。运行过程出现的最大问题是单层隔仓板篦缝易被细小钢段堵死,导致磨内通风不良。夏季温度高时,因静电吸附产生的包球包段糊衬板现象明显,不但使研磨效率大大降低,还易造成出磨水泥温度过高;冬季温度较低时,易出现饱磨现象。针对这种弊病,对隔仓板进行了改造换代。
技术改造:一仓双层隔仓板的前后层篦板外加装外框架,减少钢球对篦板的磨损。同时中心篦板的直径由460 mm增加到750 mm,孔径为5 mm×30 mm,开孔率增加到50%,提高整体通风效果。
二、三仓之间的单层隔仓板采用全新的大小圆钢棒交替设计,钢棒间距4 mm,解决了篦缝被细小钢段或铁渣堵塞的问题。中心篦板直径750 mm,孔径为4 mm×28 mm,开孔率50%,通风面积有效增大(见图3b)。把二仓钢段换成钢球,增加研磨体破碎作用,有效抑制开路磨细度跑粗现象。
在三仓衬板上增加研磨体提升装置,加大钢段运动距离,消除底层研磨体死区,让所有研磨体充分做功。将出磨中心篦板直径增大至1 000 mm,开孔率增加到50%,提高磨内通风面积,消除三仓包段糊衬板现象。
3 改造效果
通过对水泥磨系统采取以上技术改造,整体工作效率提高,磨内通风效果明显增强,水泥磨系统提产降耗明显。技改后,水泥磨台时产量提高5 t/h左右,水泥工序电耗下降2.0 kWh/t左右,取得了良好的经济效益。